Table of Contents
[ad_1]
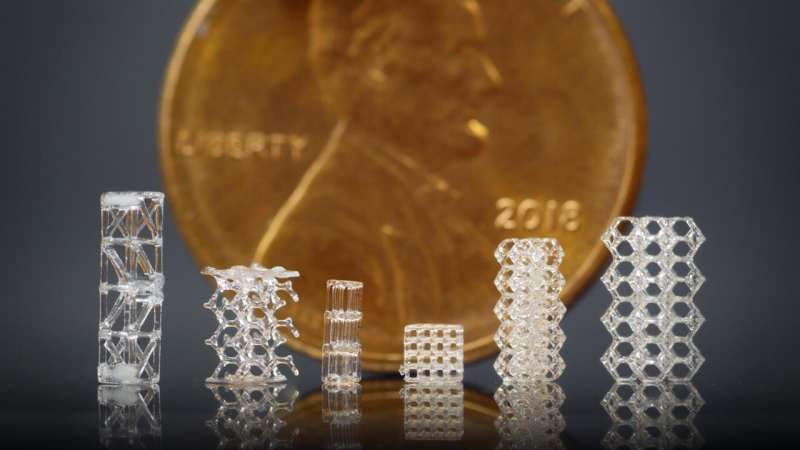
Scientists at UC Berkeley have produced a new way to 3D-print glass microstructures that is more quickly and provides objects with larger optical high-quality, style flexibility and strength, according to a new study printed in the April 15 difficulty of Science.
Operating with scientists from the Albert Ludwig University of Freiburg, Germany, the researchers expanded the abilities of a 3D-printing procedure they made a few many years ago—computed axial lithography (CAL)—to print considerably finer capabilities and to print in glass. They dubbed this new method “micro-CAL.”
Glass is the most well-liked substance for developing complicated microscopic objects, including lenses in compact, superior-good quality cameras utilised in smartphones and endoscopes, as very well as microfluidic products utilised to assess or process minute quantities of liquid. But present-day manufacturing techniques can be gradual, high priced and confined in their capacity to meet industry’s escalating needs.
The CAL process is fundamentally diverse from modern industrial 3D-printing production processes, which construct up objects from slender layers of content. This procedure can be time-intense and final result in rough surface texture. CAL, even so, 3D-prints the complete item simultaneously. Researchers use a laser to job styles of light into a rotating volume of mild-sensitive substance, constructing up a 3D light dose that then solidifies in the sought after form. The layer-less mother nature of the CAL process allows sleek surfaces and elaborate geometries.
This analyze pushes the boundaries of CAL to demonstrate its skill to print microscale attributes in glass structures. “When we to start with published this process in 2019, CAL could print objects into polymers with functions down to about a third of a millimeter in dimensions,” said Hayden Taylor, principal investigator and professor of mechanical engineering at UC Berkeley. “Now, with micro-CAL, we can print objects in polymers with capabilities down to about 20 millionths of a meter, or about a quarter of a human hair’s breadth. And for the first time, we have revealed how this approach can print not only into polymers but also into glass, with features down to about 50 millionths of a meter.”
To print the glass, Taylor and his investigate staff collaborated with scientists from the Albert Ludwig College of Freiburg, who have made a specific resin materials containing nanoparticles of glass surrounded by a light-delicate binder liquid. Digital light-weight projections from the printer solidify the binder, then the researchers heat the printed object to take out the binder and fuse the particles with each other into a sound item of pure glass.
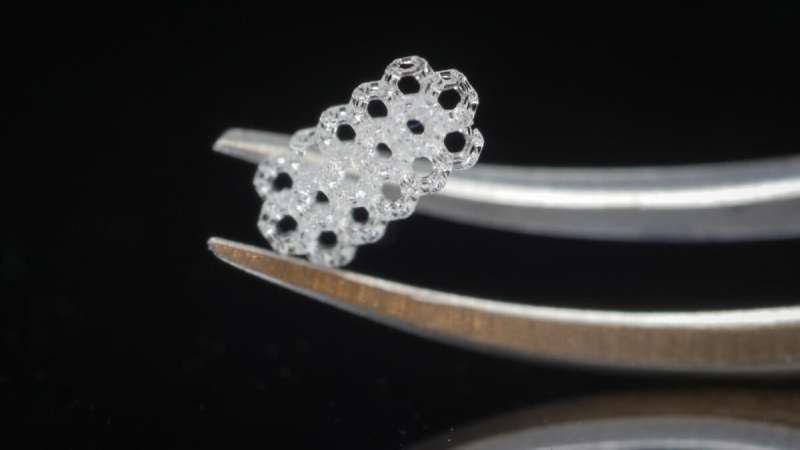
“The key enabler here is that the binder has a refractive index that is practically similar to that of the glass, so that light passes by way of the content with nearly no scattering,” said Taylor. “The CAL printing approach and this Glassomer [GmbH]-formulated product are a perfect match for each other.”
The analysis group, which bundled guide creator Joseph Toombs, a Ph.D. university student in Taylor’s lab, also ran tests and found out that the CAL-printed glass objects experienced extra consistent toughness than these made working with a standard layer-dependent printing procedure. “Glass objects are likely to crack more quickly when they comprise additional flaws or cracks, or have a tough surface,” stated Taylor. “CAL’s skill to make objects with smoother surfaces than other, layer-centered 3D-printing processes is for that reason a major opportunity edge.”
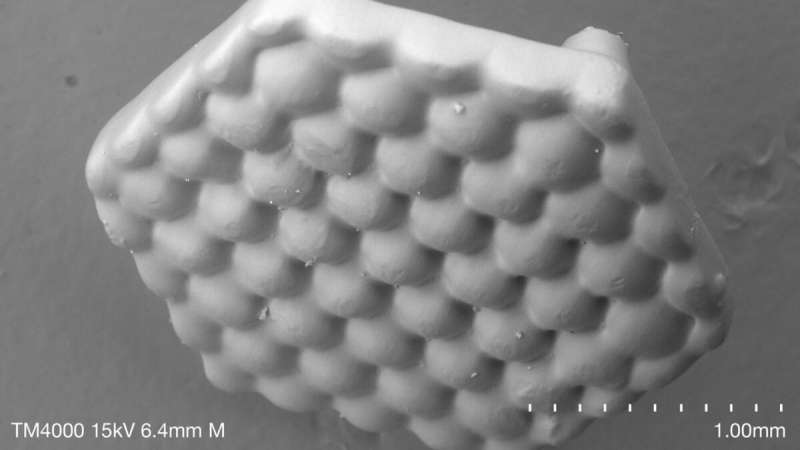
The CAL 3D-printing technique provides manufacturers of microscopic glass objects a new and much more efficient way to satisfy customers’ demanding demands for geometry, size and optical and mechanical attributes. Specially, this consists of companies of microscopic optical parts, which are a important portion of compact cameras, virtual actuality headsets, highly developed microscopes and other scientific devices. “Being equipped to make these elements a lot quicker and with more geometric independence could probably direct to new machine capabilities or reduced-expense solutions,” stated Taylor.
Joseph T. Toombs et al, Volumetric additive production of silica glass with microscale computed axial lithography, Science (2022). DOI: 10.1126/science.abm6459
Citation:
New technological innovation 3D prints glass microstructures with rays of gentle (2022, April 15)
retrieved 19 April 2022
from https://techxplore.com/news/2022-04-technology-3d-glass-microstructures-rays.html
This document is matter to copyright. Aside from any reasonable dealing for the function of personal research or exploration, no
aspect could be reproduced with no the composed permission. The information is supplied for info uses only.
[ad_2]
Supply website link